Blog
Blog>
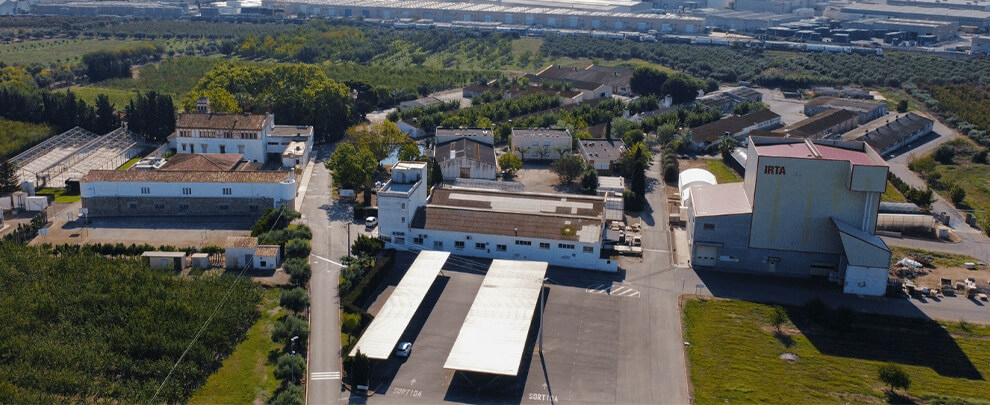
IRTA's new biogas plant, a circular economy model for pigs
01st July 2025 - News
The IRTA experimental centre in Mas Bové takes a firm step in the circular economy by constructing a biogas factory that will manage the slurry and poultry manure generated by its pig and poultry sheds to create energy and reduce the consumption of drinking water for specific uses. With a clear vision towards sustainability, the centre aims to offer a replicable model in commercial farms and a training place for biogas technicians. To find out what phase the project is at and how this plant will work, we spoke with Belén Fernández, a researcher in IRTA's biosystems sustainability programme, specialising in anaerobic digestion, biogas production and organic waste recovery.
Belén Fernández, IRTA researcher. Photo: IRTA.
How did the idea of IRTA building a biogas plant in Mas Bové come about?
The idea of building this plant arises from the need to manage the slurry and manure of the IRTA farms correctly. Specifically, the Mas Bové farms, where we have several pig sheds of different phases, from farrowing to weaning and fattening; the same happens with poultry houses. They are farms large enough, so installing a biogas plant with the amount of slurry and manure generated per year is profitable. On the other hand, we found that the equipment we had to generate heat in some warehouses was already a little outdated, so this investment is also a way to revamp them. And finally, it has coincided with the boom in interest in biogas. In addition, we have obtained a financial subsidy from the IDAE's aid for strategic biogas projects. So, for all these reasons, we considered this the right time.
How did they manage the waste generated by these farms until now?
We had a system of ponds where pig slurry accumulated and a dung heap where poultry manure was stored, and until now, we had an external supervisor who transferred all this waste to a composting plant. A part of it was destined for application in agricultural fields. This management will be slightly different because the slurry and poultry manure will be rehashed in the biogas plant to generate thermal energy after separating. Then, the digestate will be divided into two fractions. In this way, the refined fraction of the digestate will be used as irrigation water for the farms that IRTA itself has and for generalist cleaning uses within the centre, reducing drinking water consumption.
What stage is the project in?
We are now in the process of vesting the company that will build the plant. We started working on the project two years ago, and at this time, we have been investing in updating equipment for better slurry management. Modernising the ponds, constructing a composter, and installing a solid-liquid separator have already been implemented. Now we have the second part of the project, which is the construction of the biogas plant, that is, the digester, the heating system of this digester, the biogas boiler and the conditioning system of the clarified fraction of the digestate so that it has the necessary quality for irrigation or cleaning uses. Therefore, we are now finalising the permits for the construction, and the prognosis is that this summer, we will be able to start the works and that by the end of the year, between November and December, the plant will already be up and running.
How will the biogas plant work?
The treatment scheme resembles other biogas plants built next to a farm. The emptying of slurry and transporting poultry manure to a reception area will be facilitated. In one of these recovered ponds, both materials will be mixed and pumped to the digester, and there, we will work in the mesophilic range of 37º - 39º, with the idea of keeping the digester with a residence time of about 40-30 days. We have a recorded average of between 8,000 and 10,000 tonnes of slurry per year, with which we hope to produce enough biogas to generate 99 to 100 kW of heat, 10% of which we are going to use to heat the digester itself because we want to keep it at a stable temperature; the rest will be used for heating for one of the maternity sheds, which is one of the most in demand. On the other hand, after about 30 or 40 days, the rehashed material will be sent to the separator. The concentrated fraction of the digestate will be composted with part of the poultry manure to use the compost on the farm of the Mas Bové centre itself, and the clarified fraction of the digestate will go through a microfiltration and disinfection system to use for irrigation and cleaning tasks.
Once launched, does it intend to be an example of a circular economy for the industry?
Yes. In addition, everything must be recorded; that is, the non-renewable energy that we replace with renewable energy must be recorded, the amount of digest we treat, the quantities of slurry and poultry manure that enter the plant, and the compost and recovered water we obtain. IRTA is a research centre, so we love numbers and recording data and will try to record everything. In addition, it is a way of leading by example as we promote sustainability and the reduction of the impact of our activity on the environment. In this way, we can show figures, expose the pros and cons, analyse the economic viability, transfer all this information to the industry, and even train technicians on biogas installations in our field.
Is it feasible for a farmer to have his biogas plant?
The Mas Bové biogas plant will be an example of the technology available in most plants built for centralised models, where farmers manage their waste in a biogas plant. These models are more expensive, and the investment can exceed 600,000 euros. In addition, we will have another model of biogas plants built in the IRTA's EVAM milk farm, a self-consumption model. This model is more adapted to what an individual farmer may need: it would be the most coherent to install on a farm that generates between 8,000 and 20,000 tons of slurry annually. The self-consumption model is a low-cost anaerobic digester that also needs a biogas boiler, a solid-liquid separator, and a small compost within the farm to cover the stabilisation of the digestate. In this case, we would discuss an investment of close to 300,000 euros. The idea is that the two technologies installed at IRTA serve as an example for the industry, and, in each case, the most viable technology can be chosen according to the conditions.