Blog
Blog>
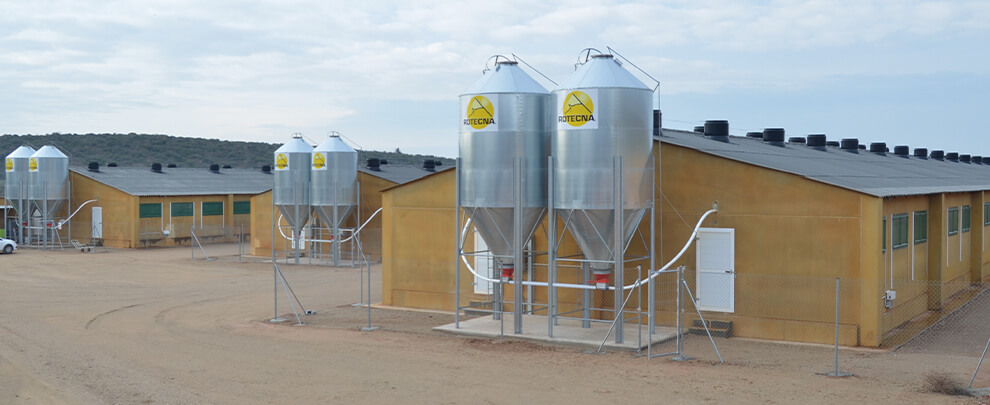
Flexible spiral feed distribution system
10th April 2024 - News
In this article, we are going to focus on flexible spiral systems, in which the line starts at the silo and ends at the motorised unit that rotates the spiral on its axis inside the tube. This fluidises the feed as it moves inside and moves from the silo to the engine. These systems are ideal for extended areas and where a high load flow rate is required.
The silo cone
Its function is to connect the silo with the transfer unit and allow it to be closed. They can be single, for one transfer unit (made of injected plastic and available with a wall of 45º for granules and 60º for flour), or double (made of plastic or fibreglass) for two transfer units. The cone and the closing squeegee allow the exit of the transfer units to be at 30º or horizontal, depending on which direction they are connected.
The C&D trasnfer unit
It is the beginning of the circuit, and one end of the flexible spiral is connected to its axis. The transfer unit is made of stainless steel, and its shaft incorporates a feed outflow control system and an inspection door with a rubber gasket to ensure no water enters. In addition, for farms where flour is supplied, a cast ball can be inserted into the transfer units to create vibration, which improves the lowering of the flour and makes it harder for the feed to clump together. transfer units can be single (single-line), double (two-line) or triple (three-line), depending on the diameters of the lines.
Rotecna uses a unique bearing system for the axle of the transfer unit, as both the bearing and the grease nipple are encased in a plastic housing for more excellent safety, as it prevents severe breakdowns in the spiral and lines. Suppose the bearing collapses due to lack of lubrication. In that case, the heat generated by the friction melts the plastic bushing, preventing the bearing from becoming entrenched and the spiral from locking at one tip, which would cause a severe breakdown. This can happen if bearings with metal bushing are used. On the other hand, when the plastic bushing melts, the system begins to make a noise when the spiral rotates, which warns that it needs to be replaced without deforming or breaking the flexible spiral or causing severe problems in the line or the transfer units. The bearing oiler is easily accessible for maintenance and greases the bearing at least once a year.
Line Tubes
The spiral lines work in traction (the spiral tends to open when rolling and pushes the transfer unit and the motor), so PVC pipes are ideal for their strength and lightness. At the beginning of the line, curves with a perfect radius can be used to minimise spiral rubbing and tube wear. The line tube diameters we work with are Ø55, Ø75 and Ø90 mm, and are made of an exceptionally abrasion-resistant material with UV protection.
Flexible Spirals
The diameter of the spiral has to be adjusted to the tube in which it is to be used, and this, in combination with the step of the spiral turn, marks the volumetric flow rate of the system. The size of the steel sheet that composes it, together with the rotation speed of the spiral, marks this flow rate. Ascending and curved sections can affect this flow rate, especially when working with flours, as they can be compressed.
Rotecna uses reinforced steel spirals with a blade size, bend radius, and return pitch specially designed to maximise flow. This flexibility minimises friction with the tubes in bends and their wear and maximises the system’s maximum length. Along the lines’ route, inside the buildings, according to the distribution of the pens, drop inlets with their respective downpipes are installed for filling ad libitum feeders or dispensers for animals with restricted feeding.
As a linear distribution system, the feeders or dispensers are filled consecutively: first, second, third, and so on until the end of the line. A sensor is installed inside the last hopper or dispenser so that the motor stops when it is complete.
Control unit
The control unit of Rotecna’s spiral distribution system is made with a stainless-steel body and translucent cone to make it easier for the farmer to inspect and check that the system is working correctly. This unit has a safety sensor that stops the motor in case the sensor placed in the last feeder or dispenser does not. The geared motor is attached to the unit’s body and rotates the spiral at about 350 rpm (revolutions per minute). The spiral is connected to it with a clamp that incorporates the reducer’s axis.
Power supply systems must be designed and sized according to the needs of each facility. In each case, Rotecna analyses and offers the best solution for the optimal feed distribution inside farms, offering reliable, efficient and safe systems.